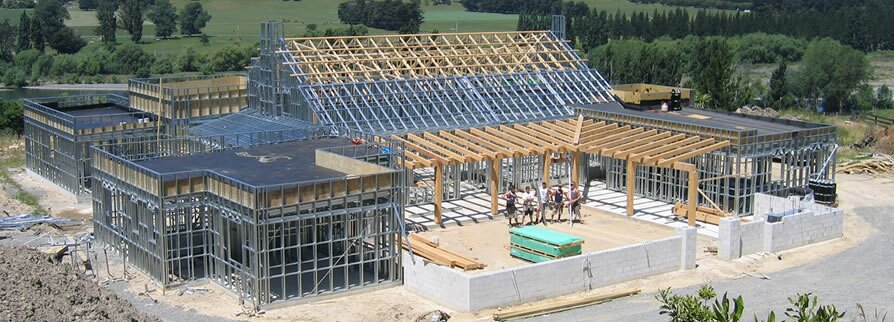
Hay distintas formas y procedimientos de fabricación de estructuras en base a perfiles galvanizados de bajo espesor que conocemos comúnmente como Steel Frame. En general, como hemos comentado, los perfiles del sistema son conformados en frío en un proceso de deformación progresiva del fleje a medida que va pasando por una serie de estaciones de rodillos de la máquina perfiladora. Este procedimiento en línea permite conformar a gran velocidad las distintas geometrías y secciones de perfiles en los distintos espesores que constituyen el sistema constructivo. Al final de la línea conformadora los perfiles se van cortando (en las dimensiones comerciales que el fabricante ofrezca), consolidando y enzunchando para su despacho a través de los distintos canales de distribución que el modelo de negocios tenga considerado. De esta forma, grandes cantidades de perfiles iguales, de largo estándar (usualmente de 2.400 o 3.000mm, aunque en virtud del proceso se pueden fabricar de cualquier medida, limitado sólo por el transporte) están disponibles para el uso en secciones habituales. Éstas son canales abiertas (para su uso principal en soleras), canales atiesadas (para pies derechos); perfiles Omega (para costaneras de cielo y/o cubiertas) y perfiles zeta (de uso como perfiles resilientes para fijar revestimientos horizontales); flejes planos para arriostramientos y otros que conforman una batería que, en conjunto con los sistemas de fijación y conexión, permiten constituir un sistema constructivo-estructural que puede resolver una gran variedad de proyectos. Los espesores varían entre 0,5mm (para elementos o particiones no estructurales) hasta 1,2 o 1,5mm, siendo el espesor de 0,85 el más común que permite resolver la gran mayoría de las demandas estructurales. En general, los perfiles son confeccionados en acero de calidad certificada (tipo ASTM 653 o similar) y son galvanizados. Conceptualmente, la estructuración del sistema constructivo se basa en una serie de tabiquerías de entramados arriostrados (con diagonales o con planchas arriostrantes como OSB o contrachapado) que pueden recibir envigados de entrepiso (confeccionados también en perfiles tipo canal de bajo espesor, muchas veces compuestos por una canal abierta y una canal atiesada que trabajan en conjunto) o estructuras de cubierta o cerchas confeccionadas también en base a esta familia de perfiles. Entre éstos, se incluyen proyectos de la más diversa escala, desde vivienda unifamiliar de uno y dos piso (más la posible mansarda) hasta construcciones mayores de equipamientos diversos hasta 3 pisos. Soluciones de mayor altura a la fecha deben recurrir a elementos estructurales complementarios, frecuentemente de estructuras principales de acero (un caso interesante de lo anterior es el edificio Altavista, publicado en este sitio en http://arquitecturaenacero.org/proyectos/edificios-de-media-altura/condominio-edificios-altavista).
Img. 1 y 2: Edificio Altavista, Marambio, San Martín y Gumucio Arquitectos, Puerto Montt, Chile
El sistema está concebido de una manera bastante similar a las construcciones de entramados de madera, como el conocido sistema de plataforma en base a piezas de madera de escuadría de 2” x 4”, muy difundido en algunos países del norte de América (como EEUU y Canadá) y de Oceanía (como Australia y Nueva Zelandia). En la práctica, se trata de un cambio de material (acero galvanizado en vez de madera) que se estructura en forma similar (soleras inferiores y superiores, pies derechos a 400 o 600mm y planchas arriostrantes). Las conexiones, por la naturaleza de los materiales, también cambian de clavos a tornillos autoperforantes. Las ventajas del steel frame sobre la construcción similar en madera pueden depender del país en país, especialmente en función del precio y de la calidad de la oferta de la madera. Aún tratando de evitar la odiosa comparación con otros materiales, es posible detallar algunas ventajas del steel frame: es absolutamente estable dimensionalmente (no sufre variaciones importantes por humedades, temperatura, exposición al aire, etc.); es de gran precisión y reduce pérdidas de material en obra; es más liviano; no sufre ataques de insectos xilófagos; es anidable (lo que tiene efecto en el montaje pero también en que reduce el volumen e transporte a la mitad); es resistente a la corrosión (por confeccionarse en perfiles galvanizados G90) y es reciclable. Éstas y otros atributos y ventajas resultan muy atractivas para abordar distintos tipos de proyectos. Mayores detalles respecto del sistema constructivo se pueden conocer en la sección de http://arquitecturaenacero.org/uso-y-aplicaciones-del-acero/soluciones-constructivas/estructuras-de-entramados-de-ac....
En las secciones de proyectos hemos tenido la oportunidad de presentar diversas obras ejecutadas en base a este sistema constructivo que resultaría largo e injusto (acaso incompleto) enumerar aquí.
En un artículo publicado hace algunos meses en este mismo sitio (ver en http://arquitecturaenacero.org/historia/teoria/steel-frame-y-entramados-de-perfiles-conformados-en-frio) terminábamos comentando brevemente el surgimiento de un desarrollo reciente o una variante de este sistema que consiste en unidades de `producción de perfiles con equipos de escala menor. Para hacer un descripción somera, este sistema demanda una máquina conformadora de pequeña escala y dimensión (no mide más de 3,0 m de largo, frente a las perfiladoras que suelen medir varias decenas de metros), alimentada por un carrete que contiene el fleje ya dimensionado (mientras en las grandes empresas de conformado, los flejes suelen dimensionarse a partir de rollos de 1.000 o 1.200mm de ancho y de un peso que supera las 5,0 ton). Estos equipos son livianos y de bajo consumo de energía. La variedad de perfiles que se producen en estos equipos es menor y, en general, se diferencian en canales y perfiles tipo omega. Todas las canales son atiesadas y llevan un pequeño destaje o replique del nervio que permite alojar los empalmes, con lo que se suple la menor variedad de perfiles. Tanto los destajes, repliegues, cortes de dimensionado y perforaciones para la instalación de los pernos de conexión se producen en la misma máquina durante el proceso de conformado. Las diferencias entre una y otra forma de producción son de escala, de variedad de productos, de velocidad de producción (las unidades que comentamos producen a una velocidad sensiblemente menor que las perfiladoras) y, especialmente de concepción o modelo de gestión. Veamos.
El Steel Frame ha sido impulsado por la industria de escala mediana o grande, proveyendo, en general, elementos estructurales (perfiles) según su portafolio de secciones, aunque siempre en secciones cercanas a los 40 x 90mm nominales que provienen de la técnica del 2” x 4” de madera. Generalmente se trata de perfiles tipo “U” o canales abiertas usadas como soleras o para formar parte de vigas compuestas; Canales tipo “C” o canales atiesadas, para ser usadas principalmente en pies derechos y componentes compuestos; Perfiles Omega, utilizados como costaneras en estructuras de cubiertas y cielos; Ángulos y Flejes. Todos ellos se producen en distintas secciones y variedad de espesores.
Img. 3: Distintas configuraciones de estructuras de cubiertas en base a cerchas y detalle de fijación. Gentileza Cintac
Img. 4:
En algunos casos, los conformadores de perfiles han extendido su oferta hasta la producción o prefabricación de componentes (tabiques, cerchas, etc.) aunque aspirando a una producción en lo posible repetitiva de componentes iguales o con una muy pequeña dispersión de alternativas. Para los efectos de la edificación, se ofrecen, pues, dos alternativas: a) la prefabricación, caso en el cual el constructor, que por las características de repetición y/o cantidad de elementos puede acceder a ello, adquiere los componentes estructurales que requiere, en una planta que los prefabrica a partir del suministro del fabricante de los perfiles y b) la construcción a pie de obra, en la que el constructor ha comprado al fabricante o distribuidor los perfiles que requiere y fabrica, en obra, los tabiques y demás componentes estructurales que su proyecto considera. Ambas condiciones de elaboración de los componentes son, parecidos. Se requiere de una mesa de armado, sobre la que se debe trazar el componente a fabricar, una zona de corte y dimensionado y sistemas de atornilladores (preferentemente mecánicos). Aunque la organización de la faena no es compleja ni demanda demasiado espacio, el trabajo en taller o en condiciones de resguardo es preferible y más productivo.
Img. 5
En el caso de los equipos móviles, la variedad de perfiles se reduce a dos (perfil estructural para tabiques y perfil estructural para cerchas) y su producción está asociada a un proyecto específico que ha sido previamente estructurado y modulado con el apoyo de un software.
En otras palabras, el equipo produce, por ejemplo, los elementos necesarios para una casa. Sin embargo, dado que el proyecto está estructurado y modelado previamente, no se están produciendo solamente elementos aislados sino elementos específicos que forman parte de un componente que constituye una unidad constructiva-estructural ya conocida. Me explico: los perfiles se van conformando a partir del fleje, con todas sus singularidades (perforaciones, destajes, repliegues y cortes) incorporadas y según la secuencia de montaje. Esto significa que a la salida de la máquina conformadora, el elemento pasa de inmediato a formar parte del componente (tabique, cercha, etc.) que se va armando a medida que se está produciendo el perfil. Para ello no se requiere, nuevamente, de una gran instalación y, en muchos casos, ni siquiera de una mesa de armado.
Img. 8 y 9:
Con frecuencia, se disponen de unos atriles en los que se van apoyando los perfiles que constituyen la estructura básica del componente y simplemente se van conectando con pernos según el calce de las perforaciones consideradas. He tenido oportunidad de observar el proceso y debo decir que los operarios casi no consultan los planos de fabricación porque la secuencia de producción es tan lógica que parece a prueba de errores: basta conectar con el perfil anterior en el punto en que exista una perforación. Otra consideración importante es que el proceso de armado del componente, no es necesario medir absolutamente nada. La precisión viene dada desde la producción del perfil y depende del software que controla tanto el diseño (a partir del proyecto de arquitectura) como la producción del elemento. Esto último no es retórica y todo aquel que ha tenido que trabajar en terreno podrá apreciar los beneficios de reducir la necesidad de medir o rectificar medidas: simplemente se reducen a casi cero los riesgos de errores dimensionales. (No digo cero errores, porque aún el mejor de los softwares y procedimientos puede producirlos). Estos equipos se pueden instalar en un taller de reducidas dimensiones o a pie de obra. El control numérico se hace con un simple notebook conectado a la máquina procesadora, que puede ser mismo equipo en el que se ha desarrollado el diseño. Como el software modela en 3D, tanto la visualización del proyecto permite detectar oportuna y tempranamente las posibles inconsistencias. Así, la demanda de grandes recursos (personal, equipos, espacio, capital, energía, etc.) se reduce drásticamente. Los procesos que he tenido la oportunidad de ver en operación requieren máximo a 3 operarios: una persona que está a cargo del software y de la producción del elemento y dos personas en el armado del componente.
Img. 10, 11 y 12: Casas el Lolol, Chile; Ampliación casa Pucón, Chile; Obras Proyecto especial de 400 m2, edificacion de tres pisos, Chile. Gentileza TecnoTruss
Es posible que el costo de cada conexión sea un poco mayor que en el caso del steel frame tradicional ya que se reemplazan los tornillos autoperforantes por pernos con tuercas y golillas, pero la simplificación y productividad del proceso de armado debería compensar este sobrecosto por unidad.
En términos de productividad habrá que contrastar el proceso completo, desde el fleje hasta la prefabricación del componente. En el caso del steel frame tradicional tenemos una muy alta productividad en la conformación del elemento, luego un período indefinido que cubre el embalado, almacenamiento en fábrica, despacho, almacenamiento en obra (si es que obviamos la cadena de distribuidores) y finalmente prefabricación del componente. Todo ello demanda tiempos (incluidos tiempos muertos no despreciables), espacio, equipos de movimiento (transporte y/o traslado) y energía asociada a esto.
Las unidades menores producen los perfiles a una velocidad sensiblemente menor, pero la (pre) fabricación del componente se hace en línea, sin demanda de almacenamiento y traslado interno. No está hecho el estudio de tiempos y costos en detalle, pero es bastante probable que la producción y prefabricación en línea termine siendo más rápida en la apreciación global, amén de ser más eficiente en términos de costos de traslado y demanda de espacios de almacenamiento. Parece una opción interesante de evaluar, también, desde la perspectiva de la sustentabilidad. El impacto en la reducción de excedentes, la reducción del espacio demandado, la reducción de la energía incorporada tanto en la conformación de los perfiles como en el traslado interno y externo, puede ser materia de un estudio más exhaustivo que arroje resultados de interés.
Respecto del montaje, no habrá diferencias entre uno y otro procedimiento y tanto uno como el otro se podrán organizar todo lo racional y eficientemente que el proyecto entero y la estructura organizacional lo permitan.
Lo anterior aborda los puntos relacionados a la escala, variedad y productividad.
Lo que me parece que cambia radicalmente es el modelo de gestión posible. El artículo sobre el steel frame comentado terminaba con una frase que parece oportuno retomar: No sería de extrañar que en el futuro próximo se observe el surgimiento de distintas unidades de producción de esta variante del Steel Frame.
La verdad es que esto en parte ya se ha estado cumpliendo. En Chile, una empresa pionera en la prefabricación en madera (Tecnotruss: entramados y cerchas de madera), que además tiene una unidad de producción de paneles SIP (Tecnopanel), ha incursionado en la producción de estructuras en base a perfiles galvanizados de bajo espesor en la modalidad comentada de unidades de escala menor: Tecno frame. El modelo de gestión de esta empresa atiende a una estrategia que también aplica con el resto de los componentes que fabrica: responder a las demandas de clientes (arquitectos, constructores o desarrolladores inmobiliarios), proveyendo un producto confiable, sujeto a un control de calidad adecuado y propio de un proceso de producción industrial bien estructurado. El quid del servicio se basa en la eficiencia de conversión, transformación y optimización del diseño original del cliente a las condiciones del sistema constructivo mediante el uso del software que desarrolla el modelo estructural y constructivo y los detalles de fabricación de los elementos y modulación de los componentes. La responsabilidad del montaje recae en el cliente. Este modelo permite a esta empresa no competir con parte de su mercado objetivo, especialmente las constructoras y gestores inmobiliarios.
Sin embargo, hay un modelo distinto de integración vertical. Surge de la alianza estratégica entre una empresa que fabrica (tanto los elementos como los componentes), construye (realiza el montaje de los componentes y la construcción completa de la obra, incluyendo instalaciones y terminaciones) con una oficina que diseña (arquitectos) que ya están familiarizados con el sistema constructivo y pueden, a partir del diseño, optimizar los recursos y ventajas que ofrece. Las empresas ARQvision Sustanaible Architecture y FASTSTEEL han realizado obras que apuntan al ahorro de recursos en las etapas de Diseño, Edificación y Operación de las construcciones realizadas.
En diseño, operando con Vector Works Designer, un software de la familia BIM, que dialoga con framecad structure que desarrolla el análisis estructural, framecad detailer que soluciona los detalles constructivos y framecad factory que comunica el diseño cad a la fábrica de estructuras.
En edificación mediante una planta móvil FRAMECAD F325IT se conecta con el software que proporciona la estructura de cualquier proyecto fabricando el Kit de componentes del edificio en pocas horas con cero perdidas y con una precisión de 0.1 mm
En operación, al optimizar el diseño arquitectónico a fin de proveer una Climatización e Iluminación Pasiva, mediante el adecuado uso de estrategias de orientación del edificio, ventilación natural y diseño y construcción de la envolvente.
Las estrategias distintas apuntan a mercados distintos, tanto entre las ofertas de las plantas menores comentadas, como respecto de la construcción del steel frame tradicional. Como vimos, modelos de gestión distintos pero también escalas distintas comparte un espectro amplio de mercado y compiten por su posicionamiento. Posiblemente las plantas móviles o de menor escala no estén en condiciones de abordar o de competir eficazmente en proyectos de gran escala o de muchas unidades repetitivas (por ejemplo, vivienda de interés social) en las que la escala (y posiblemente el costo) de las construcciones mediante el steel frame tradicional sean más competitivas. Aunque no hay que descartar que incursionen en ello. Por otra parte, la construcción del steel frame tradicional atiende perfectamente las demandas de proyectos únicos y/o menores y hasta las ampliaciones de obras, toda vez que el problema de la escala lo traslada al constructor. Sin embargo, la planta móvil puede ser una ventaja competitiva interesante en proyectos alejados o de difícil accesibilidad No corresponde a las responsabilidades de este sitio pronunciarse sobre las ventajas o limitaciones de una u otra estrategia o forma de producción del steel frame si no celebrar la innovación y la iniciativa que se aprecia en estos distintos emprendimientos que hacen del acero como material, un buen aliado a las necesidades de proyecto.
Francis Pfenniger
Arquitecto